I’ve compiled new-construction defect photos from the past six years into this one gigantic blog post. If you’re in the market for a new home and you’re not sure if a home inspection is worth doing, please look through these photos. If you’re a real estate agent who isn’t sold on the value of a home inspection on a new home, please look through these photos. If these don’t convince you, nothing will. These were all taken during pre-drywall inspections, new construction inspections, or one-year warranty inspections. If you own a new home and didn’t have it inspected before you bought it, consider having it inspected before your one-year warranty is up.
Builders should welcome the opportunity to have their homes inspected by private home inspectors; it’s a chance for construction errors to be addressed before they become major problems. It doesn’t matter how thorough the municipal inspector is; mistakes are still missed.
This is not meant as a knock against builders, municipal inspectors, or any tradespeople. This is simply meant to let new home buyers know that “new” does not mean “perfect”.
Click on any of the images below for a large version.
Water Management
A common design for new houses is to concentrate rain water from several roof surfaces to a small area, which greatly increases the potential for foundation and basement water problems. I marked up the images from some recent new construction inspections to help highlight where a lot of water gets concentrated.
In the last image shown above, all of the water from the upper roof surfaces dumps onto the lower roof, and from there, it dumps onto the corner of the deck right by the patio door. My company does a lot of invasive moisture testing in addition to home inspections, and without a doubt, one of the worst areas for water leakage is at the end of deck ledgerboards. I can almost guarantee that water is going to leak into this building before the year is up. Not only that, but this is also a recipe for basement water intrusion. To make things worse, the ground wasn’t properly pitched away from the building, and the soil was too close to the stone veneer siding.
As I mentioned in my blog post about installation errors with stone veneer siding, there should be a 4″ gap between the bottom of the stone veneer siding and the earth. How does one even fix all of this stuff? As George would say, this is a “whole bowl of wrong”. There’s not much that can be done about the roof lines at this point, but adding gutters would do wonders for this situation.
I told the buyer to have gutters added, whether he had to pay for them out of his own pocket or not. The association wouldn’t allow gutters for aesthetic reasons, and less than a month after I inspected that building, four of the units in this association ended up with basement water intrusion. The association had gutters installed shortly after that.
Installing gutters would probably help in all of the situations shown above, but gutters are something that should be planned for early on. If you’re having a home built, think about exterior water management. Take a step back and think above where all of the water will go. If gutters are going to be installed (and they almost always should be), make sure the downspouts have a good location to drain to. That means not onto a walkway, and not over a walkway. Sometimes, this involves laying down an underground drain. It’s cheap and easy to do this before the front walkways are poured. Not so much afterwards.
Here was a major oops, this time at a huge custom home in a nice suburb of Minneapolis where houses are constantly being torn down and rebuilt. The stamped concrete patio was sloped toward the house, which is a no-no.
I bring along a coiled up garden hose just for this kind of thing. A level could also be used to show that the patio isn’t sloped properly, but I think the water test is more definitive. In this particular case, to be fair to the municipal inspector (aka code official / city inspector / permit inspector / building inspector) for this home, the improperly sloped patio was not missed. As it turned out, the municipal inspector had already called this out, and the builder had a crew out to the home later the same day tearing out the whole stamped concrete while I was inspecting.
Decks
The most common deck defect that I used to find on new decks was improper nails used on joist hangers. The nail I’m holding in the photo below isn’t even half as long as it should be.
The problem with these nails is that they don’t even begin to penetrate the ledgerboard. In the photo below, you can see the tips of the nails not going into anything.
Here’s another view showing what is and what should be.
Over the last five years, I’ve found this defect less and less. Word has gotten around, and municipal inspectors are calling out this defect. Nevertheless, there are other ways to install a joist hanger improperly. Here are a few defects from this year:
The joist hangers shown below were the wrong ones for the job and won’t hold what they’re supposed to.
In the photos below, joist hangers were forgotten about or missed .
And here we have a missing metal hanger at the tripled 2x10s, which were supporting a stairway.
Stairway are frequently installed improperly. In the photo below, the stringers were cut wrong, and then someone scabbed on pieces of deck boards to try to make up the difference.
On the stairway below, each stringer was attached with two 1-1/2″ nails going into a corner bracket. No good.
In the photo below, those long metal straps aren’t doing squat.
In the next two photos, the deck stairway is attached to a piece of siding trim with deck screws. Also, there shouldn’t be openings between the risers that could allow a 4″ sphere to pass through.
At the deck pictured below, the stairway stringers were all improperly attached. As a general rule of thumb, if you see a fastener going into the end-grain of wood, it’s probably wrong. The diagram for LSC Stairway Stringer Fasteners is also shown in the photo below. Click on the photo for a large version.
The handrail shown below was too close to the guard. There needs to be at least 1-1/2″ of space. I don’t make a habit of measuring this distance, but when I go to grab the handrail and my hand barely fits, I know it’s wrong. This isn’t a big deal, and it’s not a major fix, but the point is that this is super-basic-stairway-construction-101 done wrong on a brand new home.
When nails are overdriven on the deck boards, water will sit in every one of those nail holes and lead to premature deterioration of the deck.
Would anyone accept lumber like this on a brand new deck?
When the dropoff from a deck exceeds 30″, a guard is required on the open side. The national building code require the drop to be measured 3′ out from the deck, but here in MN, the building code has been amended to remove that requirement (section R312.1.1), which I personally don’t agree with. This means that the new deck pictured below, with a 31″ dropoff measured straight down, could arguably be made code compliance by dumping down some mulch right below the open side of the deck. Would that really make it any safer? Of course not. If someone falls, it’ll be much more than a 30″ fall, because the ground slopes away. Common sense says that the open side of this deck should have a guard installed, whether it’s required by code or not.
Just one more deck item. This isn’t that big of a deal, but it was the only time I’ve ever seen something like this done. The builder left a thin little piece of each 6×6 post and bolted the beam onto it.
A metal bracket would have been more appropriate.
The diagram above comes from the Prescriptive Residential Wood Deck Construction Guide, which is fantastic. If you build decks, inspect decks, are planning to build a deck, or just want some great info on how to properly build a deck, download this free guide from the American Wood Council.
Siding
I recently wrote an entire blog post on installation defects with LP Smartside, which I won’t repeat here. All of those installation defects were from new homes. Here’s a compilation of images from that post:
Same thing goes for stone veneer siding. Here’s a compilation of installation defects from new installations, mostly from a previous blog post I wrote about installation defects with stone veneer siding:
I wrote a blog post about installation defects with James Hardie siding over six years ago, but not much in that post is applicable any longer. Installers seem to do a much better job today than they were doing back then. Nevertheless, there are plenty of installation errors still happening today with fiber cement siding. Mark Parlee, a siding guru down in Iowa, recently published an article in the Journal of Light Construction detailing numerous installation problems happening with fiber cement siding today: http://www.jlconline.com/how-to/exteriors/common-siding-failures_o
Roofs
New construction roofs are not impervious to installation defects. The most common issue we find with new roof installations is improper shingle nailing. When nails are overdriven, driven at an angle, or located too high on the shingles, it’s a defective installation. The photos below show overdriven nails on new construction homes. I have dozens, maybe hundreds of these, but they’re all pretty repetitive.
When I find a roof with overdriven nails, I recommend having the roof covering replaced, or getting a letter from the roofing manufacturer saying that these installation defects will not void the warranty. I’ve never seen that letter sent out from a manufacturer before, but I have seen full tear-offs and replacements. The photo below shows new shingles delivered on top of the existing roof that was only a week or two old. The home buyer sent me this photo to show that the builder was making good with their defective installation.
While over-driven nails are a fairly common defect at new roofs, under-driven nails can be a problem too. This prevents shingles from sealing down properly. The home shown below had a lot of them.
The fix for this isn’t as big of a deal as over-driven nails, because the nails can simply be pounded back down as long as they haven’t punched through the shingles. Once under-driven nails have punched through the shingles above, the fix is to replace the damaged shingles.
Short nails on a new roof isn’t a common defect, but I’ve found them. In the photo below, the ridge shingles were fastened with 1-1/4″ nails, which barely even touched the roof sheathing. I could pull ’em right out by hand.
I’ve found plenty of new roofs with blown off / loose shingles as well.
Believe it or not, the loose tab below was from a roof installed on a new-construction townhome in 2015. What seems odd to me is that any builders are still using 3-tab shingles 😉
Here’s a roof peak that will surely leak. Water from the seam on the right drains under the seam on the left.
Why didn’t the municipal inspectors catch these defects? Most municipal inspectors don’t walk on roofs.
Here’s a roofing defect that we were suspicious of before we even went into the attic. The roofer missed one of the roof vents. As you can tell from the house wrap, this was a defect we caught during a pre-drywall inspection.
Here’s what it looked like from inside the attic. Don’t step there.
Here’s the opposite. This new home didn’t have a single roof vent installed. Not one.
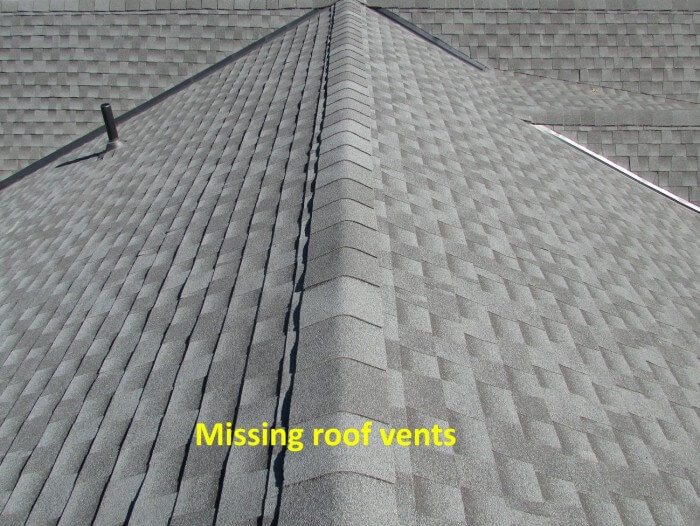
Attics
The photo below comes from the same house shown above. There wasn’t a single roof vent installed on this new home.
I generally think roof vents are over-rated, but that doesn’t mean they should be skipped. This same house had drip marks in the insulation throughout the entire attic.
The drip marks were the result of condensation/frost in the attic. Roof vents would have helped to hide this problem, which was partially caused by several disconnected bath fan ducts in the attic.
Attic air leaks between the living space and the attic are the other big cause of condensation/frost in the attic. Here’s an example of what an attic air leak looks like before everything gets covered with insulation. The space between the top wall plates was open. This is typical stuff that we find during pre-drywall inspections if we can do the inspection before the attic is insulated.
Here’s an air leak that was covered with insulation:
We found that using an infrared camera. Infared inspections are an add-on service to our standard home inspection. They make finding attic air leaks a piece of cake. Here’s an infrared image of a disconnected / missing bath fan duct below the insulation in an attic on a cool day. There were no visible signs of this defect, but a quick scan with an infrared camera made it quite obvious.
Here’s frost and black staining below in a new-construction attic. This was the result of an air leak.
When data tubes end in the attic, the ends need to be sealed off to help prevent them from pumping conditioned air into the attic like a chimney.
We’ve found many broken trusses* in new attics.
* John Bouldin, Ph.D., says that once it’s broken, you can no longer call it a truss. It’s a building component formerly known as a truss. I’ll try to come up with a symbol that they can go by.
Here’s a home where the builder agreed to install a radon fan, but installed the fan on its side. Radon fans should be installed vertically to help prevent water from accumulating, which can cause the motor to burn out prematurely.
Without a doubt, the most common problem that I find on new construction inspections is insufficient insulation in the attic. I’ve been talking about this for a long time, and I still find this defect at a lot of new homes. This is a common problem because there is no such thing as an “attic insulation inspection” for new construction homes. See my blog post dedicated to attic inspections on new construction houses: Who Inspected Your Attic?
Fiberglass batts do a terrible job of insulating attics because they’re impossible to install properly. They leave gaps all over the place. In the middle of the photo below, the insulation was compressed down to 3-1/2″ thick, which is completely inadequate. It’s not common to find fiberglass batts in new homes, but it happens.
Here’s a custom home that had fiberglass batts haphazardly installed throughout the attic, hopefully by someone who did not install insulation for a living.
Putting ductwork in an unconditioned attic is generally bad practice too: http://buildingscience.com/documents/insights/bsi-074-duct-dynasty
Just for fun, here’s an attic that I came across while doing a TISH evaluation at a vacant townhome built in 2005. There were two attic spaces here; above attic #1 was plenty of snow. Above attic #2… no snow. Someone completely forgot to insulate attic #2. I’ve heard of this happening before, but this was the only home I’ve inspected like this. In other words, this is not a common defect, but it sure is an egregious one.
If you’re buying a new construction home and the attic access panel is “sealed”, insist on having it opened. More on that topic here: Opening “sealed” attic access panels is no big deal.
Plumbing
Even new stuff can leak. We test tiled showers by using a shower dam. When tiled showers leak, it’s a big deal. This photo shows our shower dam sitting in the shower.
We use infrared cameras to check ceilings below showers for leaks, and we can usually identify shower leaks before any water is ever visible, but not always. The next photo shows water that leaked through the shower base, down into the garage.
While scanning the ceiling for a shower leak with my IR camera, I once found a leaking shutoff valve for the bathroom sink. This was a very slow leak, but the builder was very thankful that we found it when we did. This would have been a huge hassle if the ceiling had to be repaired, but we caught it before any repairs had to happen there.
Here’s a home where the new dishwasher leaked like crazy.
Here’s a leaking bath tub overflow.
Leaking shower door.
And a leaking tub. This tub actually leaked a bunch of water through the house before my inspection, and was being repaired when I arrived.
The part that the builder didn’t know about was that the water traveled across the first floor ceiling, through an exterior wall, and down into the basement. An infrared scan and a follow-up test with a moisture meter confirmed there was water in all of these places. The builder had a lot more drying out to do than first anticipated.
When the drain, waste, and vent pipes are installed at a new home, everything gets pressure tested. To do this, the plumbing vents get capped off. After the pressure testing is complete, the caps need to be removed. This is frequently forgotten about.
Plumbing vents and drains need to be pitched so water drains out. I added the blue in the photo below to show where water will end up sitting. This vent wasn’t pitched properly.
When frost-free faucets are installed, they need to be pitched downward, to allow water to drain out. We’ve inspected many new homes where the faucets were pitched upwards. More on that topic here: frost free faucets
Dishwasher drains are supposed to be looped to the underside of the countertop. This is done wrong on a lot of new homes.
We’ve found countless access panels for bath tub drains that either gave access to a solid wall, or an access hole that was comically undersized. This isn’t a big deal, as these holes could easily be made larger without the use of tools, but it’s always good for a chuckle.
Every gas appliance needs to have a union, or some method of disconnecting the gas piping after the shutoff valve. That didn’t happen here.
HVAC
I can’t believe how many HVAC photos I have. Just a quick reminder: these are all from new homes.
The two condensors below should have been installed at least 24″ away from each other, per the manufacturer’s installation instructions.
Condensors are always supposed to be installed level. When they tip like this, the refrigerant lines can get stressed.
When a condensor sits on a wall-mounted bracket, it won’t tip. That’s good practice… but it should ideally be mounted at a height that’s convenient for servicing. Unlike this one.
Just like plumbing drains and vents, high-efficiency furnace vents need to be pitched properly to help make sure there are no dips that could allow condensate to collect and obstruct the vent. I marked up the photos below to show where this didn’t happen.
Here was a scary find. This was a disconnected vent for a water heater. Someone forgot to glue this joint.
The intake pipe on a high-efficiency furnace needs to be installed at least 12″ above grade, to help prevent it from getting blocked by snow. That didn’t happen here.
I make a point of verifying which is which at the outside, because sometimes they’re switched.
Lots of air leaks on ductwork.
Here’s a leaking condensate line. Flue gas condensate is highly corrosive, so it doesn’t take long to rust the metal cabinet of the furnace.
Another condensate leak, this time from the air conditioner.
And another. This was near the floor drain.
There should never be holes between the furnace blower compartment and the burner area, because exhaust gases from the burner could be pulled into the air that gets distributed throughout the home. The hole shown below was a ‘field modification’.
When HRVs are installed, they need to be balanced. When the balancing dampers aren’t screwed in place, it’s safe to assume it hasn’t been balanced.
At this home, someone installed a damper at the HRV intake. That won’t allow the HRV to work properly. The damper needs to be removed.
Here’s an anti-tip bracket for a range that was only attached to the drywall. That won’t provide any child safety.
Here’s a dryer exhaust terminal that was caked with lint. I found this while doing a one-year warranty inspection for the owner. While this is allowed by the building code, I think the roof is a terrible place to terminate clothes dryer ducts. More on that topic here: http://www.structuretech1.com/2014/06/dont-vent-your-clothes-dryer-through-the-roof/
We’ve found several new homes, all in the same neighborhood, with kitchen fans that made a lot of noise but didn’t exhaust any air. The fans run, but the dampers at the exterior don’t open.
We’ve found numerous bath fan terminals that don’t open as well. In some cases, it’s the result of a stuck internal damper at the fan. In other cases, it’s the result of the external damper being blocked.
Check out this hood fan. We removed the interior filters and fan cover to get a better look inside, because the damper at the exterior never opened. Inside, we found flexible plastic ductwork. The only acceptable duct material from the kitchen hood fan is smooth metal.
How hot should the air coming out of your furnace be? The specs inside your furnace will tell you. At the home shown below, the air coming out was about 178° F, while the air in the home was about 73° F. That’s a 105° F temperature rise, but the furnace manufacturer called for a rise of 40 – 70° F. I wrote it up and told the buyer to have this looked into further and corrected. More on this test here: A DIY test for your furnace
After my inspection, the builder’s HVAC company told the buyer it was fixed. About 11 months later, the owner hired me to come re-inspect a few things, one of them being the furnace. I found the same problem with the furnace. Long story short, the gas regulator was defective, and the furnace had been burning a lot more gas than it should have since the day it was installed. The builder had it fixed it the second time, but it took a full year to get to that point.
And finally, here’s a collection of poorly installed registers, mostly on toe-kicks. All from new-construction homes.
This last one is more of a “carpet” defect than an HVAC defect. See if you can figure out the problem. The photo on the right is the same as the one on the left, but includes an infrared image on top.
Electrical
Before I get into electrical defects with new homes, let me preface by saying that these defects were found at many different houses. As were all of the defects in this blog post. I don’t find a ton of electrical defects on new construction inspections, but they do exist.
The circuit breaker shown below had two wires connected, but was only designed for one wire. This is known as double tapping, and falls under home-inspection-defects-101.
Here are a couple more, again from a new construction home.
The rule is the same for neutral wires. One wire per screw. Not two.
There shouldn’t be any gap between the face of the panelboard and the drywall, when used in combustible construction. It needs to be installed flush .
The potential for installation errors is inversely proportional to the potential for the error to be seen. In other words, people are more inclined to take shortcuts when they think nobody will see. Like behind the drawers below a cooktop. This outlet was hanging from the wires. At a new home. As we say here in Minnesota, uff-da.
Here’s a GFCI outlet installed in an attic. Why? How is this supposed to be reset if it trips? This is not accessible, and should not be a GFCI device.
Junction boxes always need covers, even in the attic. This one was missed.
Here’s an outlet in an attic installed more than 10′ away from the radon vent. This wiring is now required in the attic so a radon fan can be installed if needed, but if a fan needs to be installed here, the outlet box will just need to be moved. Radon fans don’t come with 10′ cords.
Here’s an improperly placed ground clamp. It needs to be slid up about an inch so it can touch the metal.
Smoke alarms need to be installed at least 4″ down from the ceiling.
Unused openings in panels always need to be covered.
Cable clamps need to be used to secure cables to the box, and to help prevent damage to the cables. This one was missed.
Here was a super-rare find. This was a bathroom outlet that lacked GFCI protection.
Here was another rare find for a new home; a living room outlet with reversed polarity.
And finally, this chandelier was installed too close to the tub. It needs to be at least three feet away. That piece of orange tape on the ceiling marks 3′. More info on this defect here: Chandeliers above bath tubs
Structure / Basement stuff
That notch for a toilet is a no-no.
So is this one, but that’s not a notch. They went all the way through.
So is the notch in this beam. Probably.
A change to the original plans ended up leading to some major field alterations to the manufactured assemblies formerly known as trusses. We caught this during a pre-drywall inspection.
Here’s an improper hanger that has been bent up and kinda nailed into place. Kinda.
Here’s another improper hanger.
And another. Well actually, that’s not even a hanger.
This wall completely missed the anchor bolt, or the anchor bolt was improperly located.
These next two photos show obvious installation problems with the foam insulation at the rim space. More info on this topic at the Journal of Light Construction: Spray Foam Insulation Problems
When a home is built with an exhaust-only ventilation system and the poly on the wood framed portion of the basement wall isn’t perfectly sealed, humid outdoor air will leak into the basement wall cavity and then condense on the relatively cold poly. There was so much condensation on the poly at the home pictured below that water was pooling at the base of the wall. The builder had already attempted to fix a supposed leak at the window twice, but this was simply condensation.
Side note: This is the opposite of what I blogged about here: Why do houses cry? Siding stains show up during cold weather at the upper levels of the home, and ‘supply-only’ ventilation will exacerbate this condition.
The fix is to make the poly 100% airtight, or to insulate the wood-framed portion of the wall with closed-cell spray foam insulation. For the record, I’m no hypocrite; I had that done at my own house many years ago: Spray foam insulation at Reuben’s house.
That’s all for this year, and this is probably my last mega-post on new construction defects. In the future, my blog posts on new construction defects will probably be focused on one or two specific issues, and getting into the specifics of why they matter.
Thank you for reading.
Author: Reuben Saltzman, Structure Tech Home Inspections
John Battaglia
November 11, 2015, 6:12 am
Great post Reuben! It is amazing how many people think they don’t need an inspection on a new home because “the municipal inspector will catch anything that’s wrong.” I’ve been inspecting a lot of new homes this Fall down here in Atlanta and the quality of construction is some of the worst I’ve ever seen. National builders, custom builders – all really rough. Seems like they all got so busy they were handing a hammer to anyone who they could get on site!
ken
February 3, 2016, 6:18 am
In electrical panels, many terminal are rated accept two wires under one screw-both wires should be the same gauge.
Reuben Saltzman
February 3, 2016, 6:35 am
It’s true that some circuit breakers are designed to accept two wires, but as mentioned in the text, these circuit breakers were only designed to accept one.
ken
February 3, 2016, 6:26 am
Electrical box can be sitting back 1/4 inch from drywall surface, but not more. If surface material is combustible, it must be flush.
Reuben Saltzman
February 3, 2016, 6:41 am
Ken – that’s not correct. See NEC section 312.3:
“In walls of concrete, tile, or other noncombustible material, cabinets shall be installed so that the front edge of the cabinet is not set back of the finished surface more than 6 mm (1/4″.). In walls constructed of wood or other combustible material, cabinets shall be flush with the finished surface or project therefrom.”
The key term here is “wall”, not “wall surface”. With wood framed walls, the panelboard must be flush with the drywall surface; not recessed at all.